Flextran Technology
Flextran is an innovative material that is used in various industries. Flextran's production technology combines a high degree of automation and precision of processes, which makes it one of the most efficient and promising materials on the market. It itself consists of polyurethane, pleasant and smooth to the touch.
The flextran production process includes several stages:
1) Preparation of raw materials: to create a drawing, special polymer compositions are needed, which are then subjected to heat treatment and molding. The main stage of production is extrusion, the process of forming a film from molten material under pressure.
2) Next comes the stage of applying a special coating to the film, which makes the material very durable: resistant to moisture, ultraviolet radiation, etc
3) After coating, the material undergoes a cooling process and is cut into separate sheets or rolls.
Flextran technology has increasingly been used in the manufacture of clothing. For the first time it was used by the MANEKEN brand, and then others picked it up, for example, in Russia flextran is used by brands such as MONOCHROME, TRES. Also, OZON and TINKOFF companies used flextran technology to create their own merch.
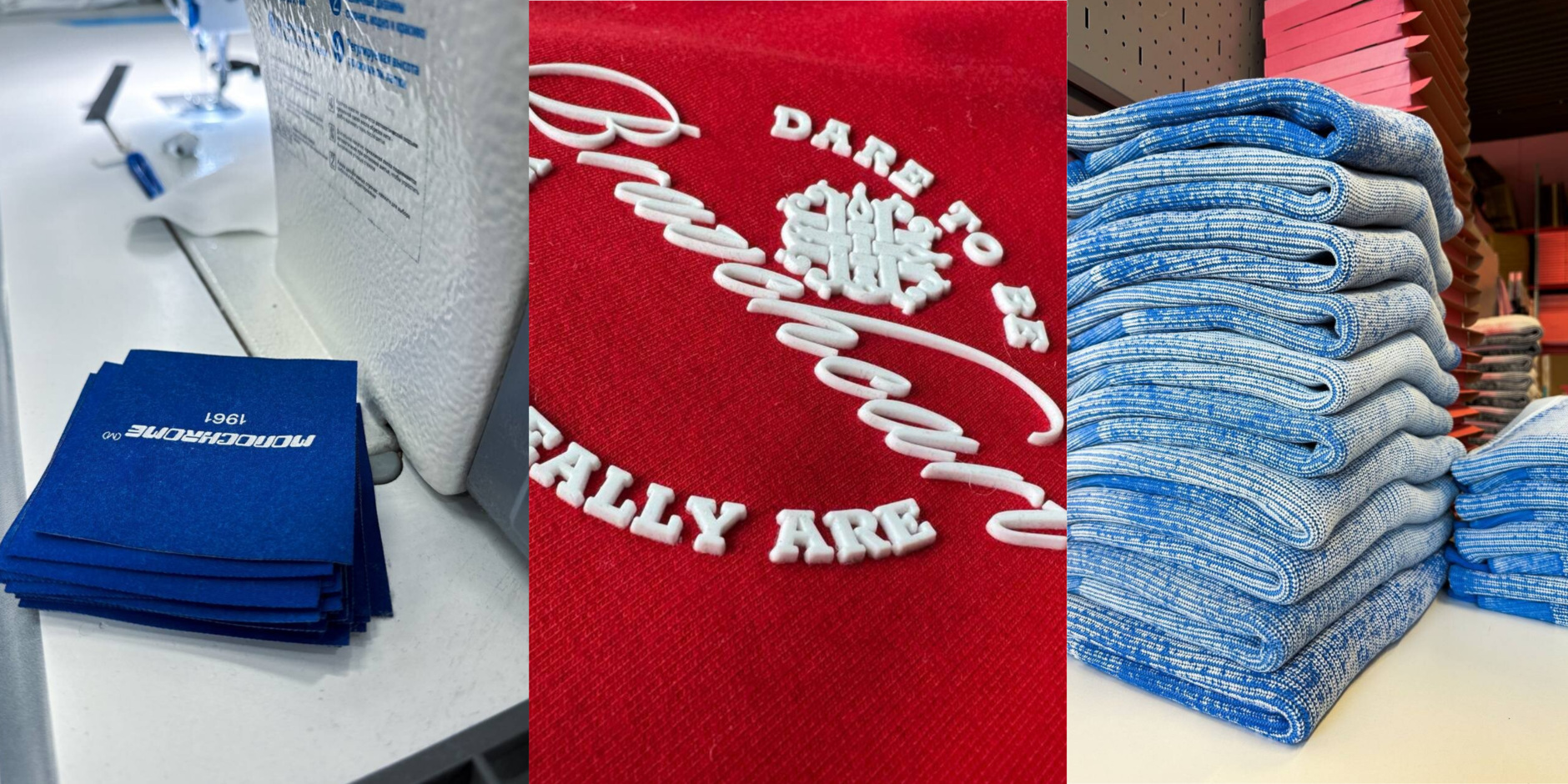
The cost of flextran is high, it will depend on the circulation and complexity of the layout, since all small elements are selected manually. Of course, flextran technology has its advantages and disadvantages.
Flextran Advantages:
– High quality– Durability (waterproof, retains color)
– durability (withstands repeated washing)
Disadvantages of Flextran:
– it is impossible to apply on some products (baseball caps, on fabrics coated with water-repellent impregnations)
– short shelf life (the shelf life of ready-made transfers is no more than 2 months)
– high price
Do you want to keep up to date with the main events in the fashion industry and brand news?